Detroit Marathon Heavy Oil Upgrade Project
Client:
Detroit, Michigan
Marathon
Location:Detroit, Michigan
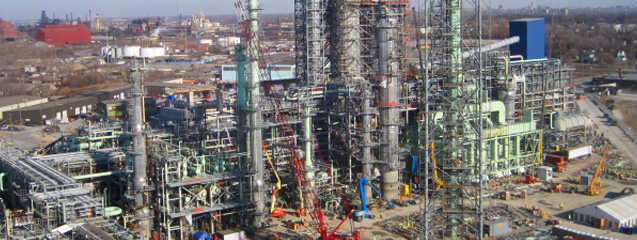
In 4Q2007, Marathon Petroleum (MPC) awarded Fluor an engineering, procurement, and construction (EPC) contract to expand the existing Detroit refinery to allow it to process additional heavy Canadian Crudes. At $2.2 billion dollars, this was a true mega project that would draw heavily on Fluor’s global expertise, and above all its capacity for distributed execution. In addition to the crude slate changes, the refinery’s capacity was increased by 15 percent to 120,000 barrels per day (bpd) through the addition of 13 new and revamped units, along with associated utilities and offsite facilities. Further, the project design included utilizing the best current technologies to reduce emissions below the EPA mandated regulations. The resulting increased production, by an additional 400,000 gallons of clean transportation fuels per day, has provided for a more stable supply of petroleum products for the state of Michigan and surrounding Mid-Western states.
Engineering and construction on the Detroit Heavy Oil Upgrade Project (DHOUP) commenced in 2008 during the peak of a heated market cycle. Engineering was performed in 6 different locations that included 5 offices: Southern California, Madrid, Mexico City, New Delhi, Mt. Laurel, and the Detroit jobsite. The project required over 1,000 pieces of equipment and large quantities of bulk materials, all procured from 7 primary global fabrication and supply areas. Offsite “Modularization” of process facilities was a key execution strategy implemented as 51 large process modules were fabricated and barged from ICA Fluor’s mod yard located in Tampico, Mexico. However, during the downturn of 2009, the construction execution strategy was significantly altered to utilize as many local contractors as possible. This was largely accomplished through the full implementation of Fluor’s suite of construction tools to define, communicate, control and monitor, the work performed.
The project team successfully accomplished each and every goal established at the kick-off of the project for safety, schedule, cost and quality, as well as stretch goals set for predictability and transparency. The MPC and Fluor teams were successful in developing a “one team mindset” by way of a close working relationship that developed through trust built on daily communication.
Engineering and construction on the Detroit Heavy Oil Upgrade Project (DHOUP) commenced in 2008 during the peak of a heated market cycle. Engineering was performed in 6 different locations that included 5 offices: Southern California, Madrid, Mexico City, New Delhi, Mt. Laurel, and the Detroit jobsite. The project required over 1,000 pieces of equipment and large quantities of bulk materials, all procured from 7 primary global fabrication and supply areas. Offsite “Modularization” of process facilities was a key execution strategy implemented as 51 large process modules were fabricated and barged from ICA Fluor’s mod yard located in Tampico, Mexico. However, during the downturn of 2009, the construction execution strategy was significantly altered to utilize as many local contractors as possible. This was largely accomplished through the full implementation of Fluor’s suite of construction tools to define, communicate, control and monitor, the work performed.
The project team successfully accomplished each and every goal established at the kick-off of the project for safety, schedule, cost and quality, as well as stretch goals set for predictability and transparency. The MPC and Fluor teams were successful in developing a “one team mindset” by way of a close working relationship that developed through trust built on daily communication.
Client's Challenge
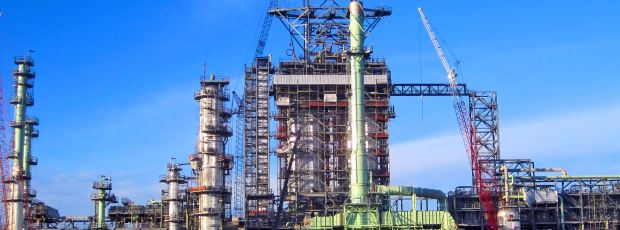
To enhance profitability of the fifth largest refiner in the United States, MPC’s goal was to process a significant amount of price advantaged heavy Canadian crude. This was accomplished by adding a new 28,000 bpd Delayed Coking Unit, a new Sulfur Complex and a new 36,000 bpd Distillate Hydrotreater. These new facilities, including the existing process units upgrades, helped to convert the heavier oil sands material into clean burning transportation fuels. This project positioned the Detroit refinery, the only refinery in Michigan, to continue to provide increased clean fuel petroleum products to Michigan and other states in the U.S. Great Lakes region. The primary challenge was to bring seamless execution of the global design and procurement efforts to support the construction of the new and revamped facilities into the operating refinery. This complex integration of new and revamped facilities was accomplished through a mid-project refinery shutdown in 2010, a two-year interim operational period, concluding with a refinery-wide shutdown in 4Q2012. The 2012 shutdown was the largest in the history of the Detroit refinery. The timely integration of the facilities, in a safe and cost effective manner, with the on-time start-up coming out of the 2012 shutdown, was paramount to the success of the project.
Solution
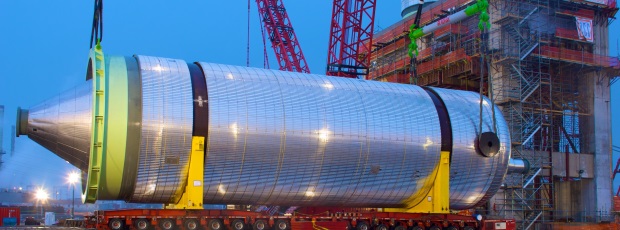
To perform the work effectively in this over-heated market, Fluor utilized six different locations for the design of this project. Fluor’s collaborative communication systems, processes and design automation tools were keys to successfully coordinating the collective efforts of the globally distributed engineering execution, global procurement and module fabrication efforts, and site investigation surveys of the existing facilities. To ensure a high degree of quality in the performance of such a significant amount of new and revamp work, detail planning from the outset, aligning of the EPC schedule with the critical site milestone completion dates, and early identification of existing refinery conditions, were required.
To help compliment the local craft workforce, that would ultimately peak at well over 2,000 personnel, Fluor utilized modular construction in the various construction areas. Large modules were fabricated for process areas and piperacks in portions of the delayed coking unit, sulfur complex and distillate hydrotreater, including selective offsite and utility facilities.
Fluor utilized some of the world’s most innovative construction technologies and tools for this project in performance of the work at site. On the initial critical path was the setting of the coke drums, accomplished in setting an industry time record, 19 weeks from first pile to setting of the drums. To support the change in construction execution by utilizing a maximum amount of local contractors, Fluor applied their MasterPlant® Suite of Project Automation Tools to improve communication and quickly create construction work packages while working with MPC to award the work to over 40 local contractors. Fluor utilized their 3D CAD plant review stations at the jobsite to help visualize and effectively status and manage the construction effort. These tools were used at the weekly subcontractor coordination meetings, providing a clear road map for the subcontractors to plan and communicate their respective work fronts.
HSE on the DHOUP project was world class. The project successfully integrated Fluor’s HSE program with MPC’s HESS program to successfully manage the labor onsite. Fluor’s commitment to health, safety, and environment resulted in more than 8 million work hours of self perform and subcontracted labor onsite without a lost-time incident and 2 million hours without a recordable incident.
To help compliment the local craft workforce, that would ultimately peak at well over 2,000 personnel, Fluor utilized modular construction in the various construction areas. Large modules were fabricated for process areas and piperacks in portions of the delayed coking unit, sulfur complex and distillate hydrotreater, including selective offsite and utility facilities.
Fluor utilized some of the world’s most innovative construction technologies and tools for this project in performance of the work at site. On the initial critical path was the setting of the coke drums, accomplished in setting an industry time record, 19 weeks from first pile to setting of the drums. To support the change in construction execution by utilizing a maximum amount of local contractors, Fluor applied their MasterPlant® Suite of Project Automation Tools to improve communication and quickly create construction work packages while working with MPC to award the work to over 40 local contractors. Fluor utilized their 3D CAD plant review stations at the jobsite to help visualize and effectively status and manage the construction effort. These tools were used at the weekly subcontractor coordination meetings, providing a clear road map for the subcontractors to plan and communicate their respective work fronts.
HSE on the DHOUP project was world class. The project successfully integrated Fluor’s HSE program with MPC’s HESS program to successfully manage the labor onsite. Fluor’s commitment to health, safety, and environment resulted in more than 8 million work hours of self perform and subcontracted labor onsite without a lost-time incident and 2 million hours without a recordable incident.
Conclusion
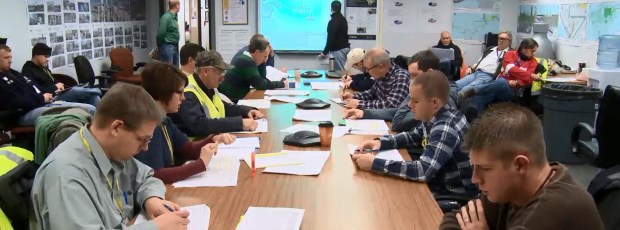
Design, procurement and module fabrication were coordinated globally. Detailed planning, along with real time updates, was essential to keeping all project personnel and activities aligned throughout the life of the project. Construction personnel embraced the use of new technologies that allowed for the safe and efficient installation of the new and revamped facilities. Fluor’s construction tools helped successfully coordinate the activities of over 40 different subcontractors, strengthening the local contractors during a significant economic downturn. Working as a single team, challenges were met “head-on” as schedule and budget was maintained. Construction on the DHOUP project began in 2008 and was completed on schedule in 3Q2012, culminating with the 4Q2012 shutdown and successful start-up.
The project successfully demonstrated a strong working relationship between MPC, Fluor, local contractors, and community to produce a project, with world class performance, that would provide additional transport fuels for the local market and support the community’s growth.
The MPC Detroit Heavy Oil Upgrade Project successfully accomplished each and every goal established at the kick-off of the project. Safety, schedule, cost, quality, predictability and transparency were all achieved. The MPC and Fluor teams formed an “integrated management team”, built on trust and accomplished through effective and regular communications and an adopted mindset of, “Say it Early, Say it Straight, Say it All.”
Read about other Fluor Constructors projects.
The project successfully demonstrated a strong working relationship between MPC, Fluor, local contractors, and community to produce a project, with world class performance, that would provide additional transport fuels for the local market and support the community’s growth.
The MPC Detroit Heavy Oil Upgrade Project successfully accomplished each and every goal established at the kick-off of the project. Safety, schedule, cost, quality, predictability and transparency were all achieved. The MPC and Fluor teams formed an “integrated management team”, built on trust and accomplished through effective and regular communications and an adopted mindset of, “Say it Early, Say it Straight, Say it All.”
Read about other Fluor Constructors projects.